Springs Window Fashions has the capacity to create millions of custom products for its customers based on a variety of styles, fabrics, sizes, and colors. The company needed a demand planning solution that could support that granularity and reflect changes in demand based on promotions. By replacing a legacy solution with Valizant Solutions on Anaplan, Springs generates demand plans four times as frequently with much greater detail and has improved forecast accuracy by 30% at levels where the business impact is greatest.
Where the business benefit is greatest, demand forecast accuracy with Anaplan solutions from Valizant has improved more than 30%.Mickey Klicka, Manager, Financial Systems
Weekly
demand plans, formerly completed monthly, provide greater business agility
30%
improvement in demand forecast accuracy at lower, granular levels, where business benefit is greatest
Greater
capacity for analytical projects that support improved business performance
Springs Window Fashions, a Wisconsin-based manufacturer of configure-to-order residential and commercial window treatments, is known as “The Best Experience Company.” To provide consumers with an outstanding customer experience, the company offers products in a vast array of styles, colors, textures, dimensions, and functions, resulting in millions of possible combinations. Although that huge product mix is a delight for customers, it represents a challenge for the company’s supply chain planners, who must ensure that the right materials, products, and labor are always available to meet customer demand.
The planners’ work is complicated by the fact that a significant portion of Springs’ demand is influenced by consumer promotions. The company’s legacy demand planning solution did a good job of forecasting demand for non-promotional products—which comprised less than half of the business.
To fill the gap, demand planners spent hours using offline analytics and manual entry adjustments to translate forecasts into operational plans, but those were still high-level. Leaders at Springs Window Fashions knew that significant performance improvement could only come from improving lower-level forecast accuracy.
Four times as fast, three times as complex
Springs chose Anaplan as the foundation for a new demand planning solution and engaged Anaplan Partner Valizant to help develop it. Valizant worked with the demand planning team and with organizations across the business to ensure alignment, create a shared vision for the solution, and build collaborative business processes.
“The Springs solution provides a seamless and highly responsive experience through all aspects of the demand planning process,” said Ed Lewis, president and CEO of Valizant. “It supports promotions planning, statistical forecasting, and collaborative demand planning across all layers of the organization.”
The solution was completed in just six months. “Compared to other implementations for our exact same business, Anaplan solutions from Valizant were up and running in a quarter of the time,” said Mickey Klicka, Springs Window Fashions’ Manager, Financial Systems. “And the solution delivered is probably three times as complex.”
Promotional calendars and events are managed in Anaplan for each key account so that past promotional activity and retail sales data are captured and used to project demand driven by the new calendar and set of events.
Now, plans for regular and promotion-based demand are generated on one Anaplan platform. Plans are accessible across the business, so operations managers, purchasing personnel, and other teams can organize their work accordingly.
More frequent, detailed, and accurate planning and forecasting
With Anaplan solutions from Valizant, Springs has moved from monthly demand planning to a weekly cycle. In addition to forecasting more frequently, 25% of products are now forecast at a lower level—and despite these increases in frequency and product granularity, the forecast accuracy with Anaplan matches that of the former high-level forecast. “At lower, more granular levels, where the business benefit is greatest, demand forecast accuracy with Anaplan solutions from Valizant has improved more than 30%,” Klicka says.
“With Anaplan, our demand planners are proactive instead of reactive,” Andy Hubred, Springs Window Fashions’ Chief Financial Officer says. “They are not only completing the planning cycle within the week, but they have capacity to take on analytical projects that support better business performance.”
The benefits of the solution extend beyond the demand planning department. The forecasts provide manufacturing facilities with a view of future labor, fabrication, and assembly needs; assist with purchasing and inventory management, particularly for critical materials with long lead times; and provide relevant raw material requirements to Springs’ vendors to eliminate production delays.
For Springs, the key to the project’s success was engaging users across the business in designing the forecasting system. The demand planning team appreciated not being constrained to the predefined methods of conventional tools, and the company as a whole has recognized that the Anaplan Connected Planning solution can support key business processes beyond demand planning.
“Anything that we could think up to configure within Anaplan, we could do,” Klicka concludes. “We can keep adding to it and extending it.”

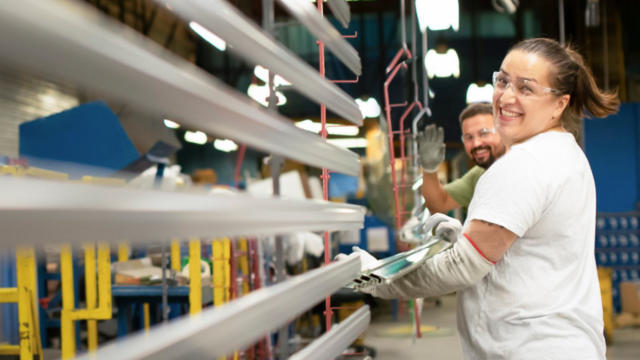